Extrusion
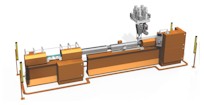
During the extrusion
process, plastic in the form of pellets or powders is fed into
a heater barrel where rotating screws homogenize and squeeze
it through a die to form a finished or semi-finished product.
|
|
Injection
Moulding

In
injection moulding, the plastic is forced into a mould at
very high pressure. The mould is kept at a given temperature
while polymer solidifies. The two halves are then opened
and the finished product is ejected.
|
|
Blow Moulding
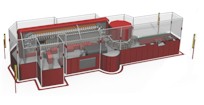
In the blow moulding process, a molten matrix is extruded
in the form of a vertical tube (parison), which is clamped
between two halves of a mould. This tube is inflated with
air so that it takes the shape of the mould. It is then cooled
and released as a fully formed product.
|
|
Thermo-Forming
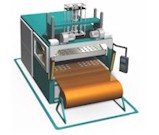
Thermo-forming
is the general term used for the process of making plastic
parts from a sheet of plastic through a combination of air
pressure and temperature change. In it's most sophisticated
form, thermo-forming can provide the precise properties and
sharp detail required to meet very stringent specifications.
|
|
Blown
Film
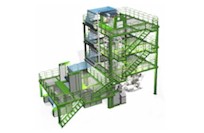
This
is the most common way of manufacturing film. A plastic blend
is fed into an extruder where it is melted and homogenized
before being pumped through a circular blown film die. The
melted plastic forms a continuous tube which is drawn from
the die. It is inflated and simultaneously cooled with fast
moving air, allowing the plastic to solidify quickly. The
tube is then collapsed between rollers and wound onto a reel. |
|
|